Flowable Fill Refusal: Common Causes and Solutions Why Flowable Fill Projects Fail: Quick Fixes Preventing Flowable Fill Refusal: Expert Tips Flowable Fill Refusal Explained: Avoid Costly Mistakes How to Tackle Flowable Fill Refusal Effectively

Flowable fill is a versatile and efficient material used in construction projects, but it’s not immune to issues. One of the most common problems contractors face is flowable fill refusal, where the material fails to set or perform as expected. This can lead to costly delays and rework. Understanding the causes and solutions is crucial for any project manager or contractor. In this post, we’ll explore why flowable fill projects fail, quick fixes to common issues, expert tips for prevention, and how to tackle refusal effectively. (Flowable Fill Refusal, Flowable Fill Failure, Construction Materials)
Why Flowable Fill Projects Fail: Quick Fixes

Flowable fill refusal often stems from improper mixing, incorrect material ratios, or inadequate preparation of the subbase. Improper mixing can result in a mixture that’s too dry or too wet, leading to poor compaction or settling. Incorrect ratios of cement, water, and aggregate can compromise the material’s strength and flowability. Additionally, a poorly prepared subbase, such as one with debris or uneven surfaces, can prevent proper bonding.
To address these issues:
- Verify Mixing Ratios: Always follow manufacturer guidelines for water-to-cement ratios.
- Test Consistency: Use a slump test to ensure the mixture is neither too dry nor too wet.
- Prepare the Subbase: Clear debris and ensure the surface is compacted and level.
📌 Note: Always consult the material supplier for specific mixing instructions to avoid refusal.
Preventing Flowable Fill Refusal: Expert Tips
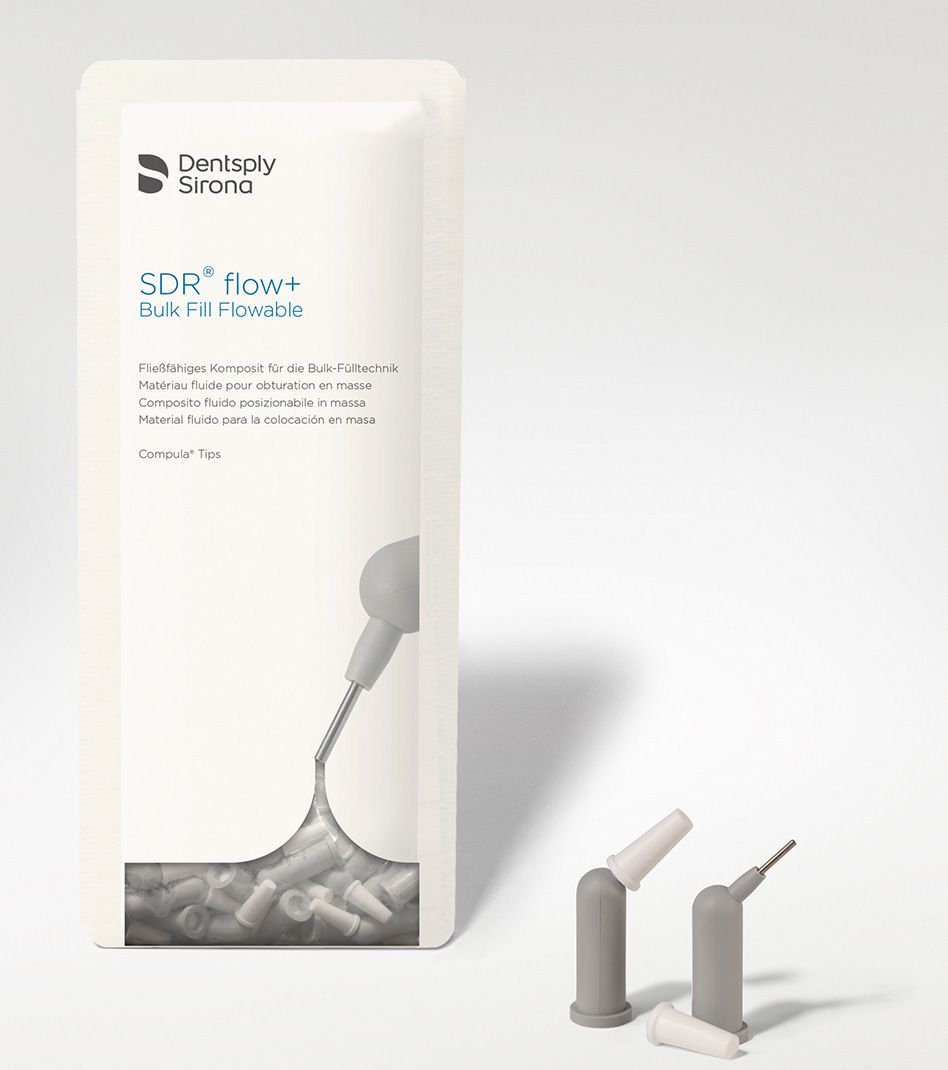
Prevention is key to avoiding flowable fill refusal. Start by conducting a site assessment to identify potential issues like poor drainage or unstable soil. Use high-quality materials and ensure they are stored properly to avoid contamination. Train your team on proper mixing and placement techniques to minimize human error.
Here’s a checklist for prevention:
- Inspect the site for drainage and soil stability.
- Store materials in a dry, covered area.
- Train workers on correct mixing and placement procedures.
- Monitor weather conditions to avoid placing fill in extreme temperatures.
Flowable Fill Refusal Explained: Avoid Costly Mistakes

Flowable fill refusal occurs when the material fails to achieve the desired strength or consistency. Common mistakes include overworking the mixture, ignoring curing time, or using contaminated water. Overworking can introduce air pockets, while insufficient curing weakens the material. Contaminated water can react negatively with cement, compromising the mix.
To avoid these mistakes:
- Minimize mixing time to prevent overworking.
- Allow adequate curing time as per manufacturer recommendations.
- Use clean, potable water for mixing.
How to Tackle Flowable Fill Refusal Effectively

If refusal occurs, act quickly to minimize damage. Assess the cause by inspecting the mixture and subbase. If the issue is poor compaction, rework the area with proper techniques. For incorrect ratios, remove the material and remix with the right proportions. In cases of contamination, replace the affected material entirely.
Steps to tackle refusal:
1. Identify the root cause (e.g., poor mixing, contamination).
2. Remove or rework the affected material.
3. Reapply flowable fill following best practices.
4. Monitor the area to ensure proper curing and settling.
What causes flowable fill refusal?
+Common causes include improper mixing, incorrect material ratios, poor subbase preparation, and contamination.
How can I prevent flowable fill refusal?
+Follow manufacturer guidelines, prepare the subbase properly, use high-quality materials, and train your team on correct techniques.
What should I do if flowable fill refusal occurs?
+Identify the cause, remove or rework the affected material, and reapply flowable fill following best practices.
Flowable fill refusal can be a frustrating and costly issue, but with the right knowledge and preparation, it’s avoidable. By understanding common causes, implementing quick fixes, and following expert tips, you can ensure your flowable fill projects succeed. Always prioritize proper mixing, subbase preparation, and material quality to minimize the risk of refusal. With these strategies, you’ll save time, money, and resources while delivering high-quality results. (Flowable Fill Solutions, Construction Best Practices, Material Refusal Prevention)