Understanding Aluminum Alloys: Melting Points Explained Aluminum Alloys: Key Melting Point Insights Melting Points of Aluminum Alloys: A Quick Guide Essential Melting Point Data for Aluminum Alloys Aluminum Alloys and Their Melting Points Simplified
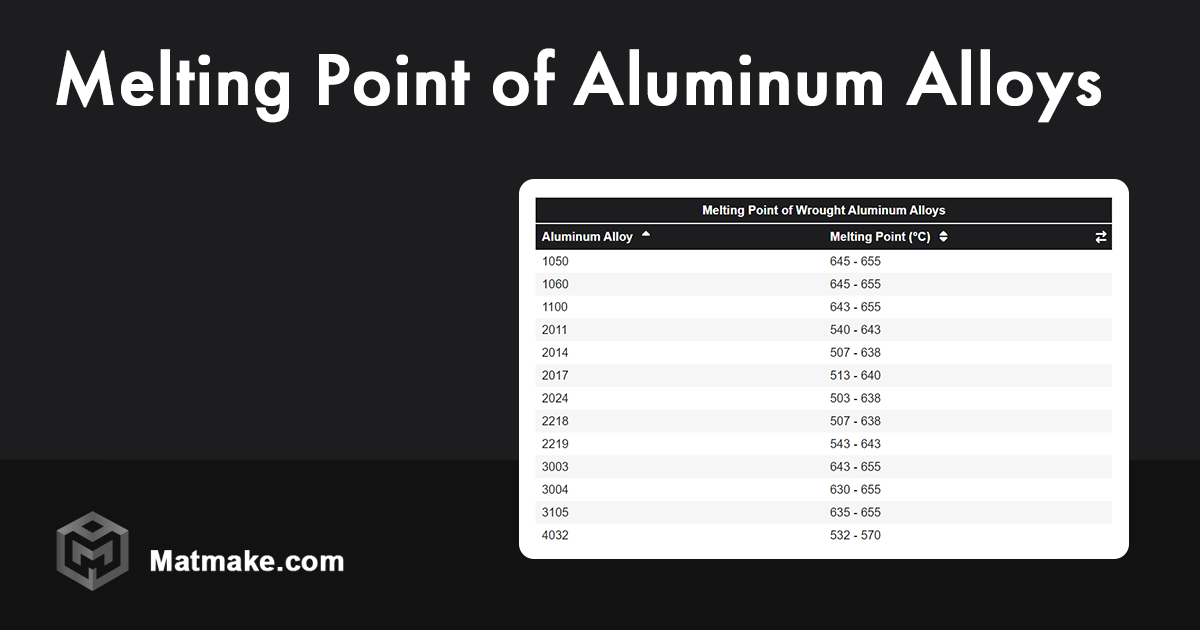
Aluminum alloys are widely used in industries ranging from aerospace to automotive due to their lightweight, strength, and corrosion resistance. One critical property that engineers and manufacturers must consider is the melting point of these alloys. Understanding the melting points of aluminum alloys is essential for processes like welding, casting, and heat treatment. This guide will break down the key insights into aluminum alloy melting points, providing both informational and commercial value for readers.
Aluminum Alloys: Key Melting Point Insights
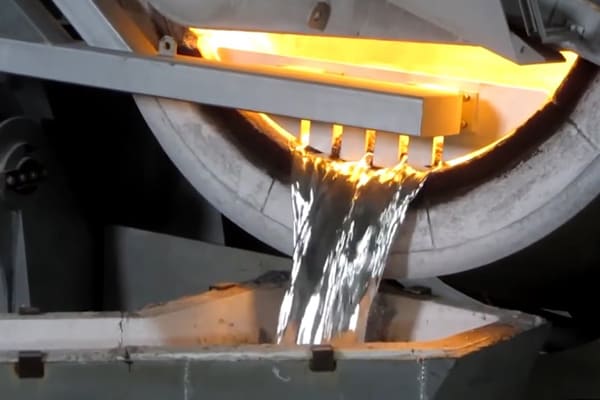
Aluminum alloys are not a one-size-fits-all material. Their melting points vary based on composition, with elements like copper, magnesium, and silicon significantly influencing this property. Pure aluminum melts at approximately 660°C (1220°F), but alloys can range from 585°C to 650°C (1085°F to 1202°F). This variation is crucial for selecting the right alloy for specific applications.
Factors Affecting Melting Points
- Alloying Elements: Copper and silicon lower the melting point, while magnesium can increase it.
- Purity: Higher purity aluminum has a more consistent melting point.
- Grain Structure: Finer grains can affect heat distribution during melting.
📌 Note: Always refer to the alloy’s datasheet for precise melting point information.
Melting Points of Aluminum Alloys: A Quick Guide

Here’s a concise table of common aluminum alloys and their melting points:
Alloy Series | Melting Point (°C) | Common Applications |
---|---|---|
1XXX (Pure Aluminum) | 660 | Packaging, electrical conductors |
2XXX (Copper Alloys) | 585–620 | Aerospace, high-strength structures |
6XXX (Magnesium-Silicon Alloys) | 585–650 | Automotive, architectural extrusions |
7XXX (Zinc Alloys) | 475–635 | Aerospace, high-performance parts |

Essential Melting Point Data for Aluminum Alloys

For commercial applications, knowing the melting point is vital for manufacturing processes. For instance, welding requires precise temperature control to avoid weakening the alloy. Similarly, casting demands accurate melting points to ensure proper mold filling.
Commercial Applications Checklist
- Welding: Match the alloy’s melting point with the welding technique.
- Casting: Use alloys with lower melting points for complex molds.
- Heat Treatment: Avoid exceeding the melting point to maintain structural integrity.
Aluminum Alloys and Their Melting Points Simplified
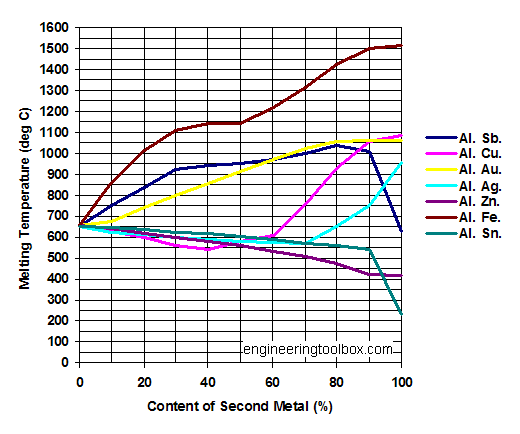
In summary, aluminum alloys offer versatility, but their melting points must align with the intended application. Whether you’re an engineer, manufacturer, or hobbyist, understanding these properties ensures optimal performance and longevity of the material.
💡 Note: Consult material experts for specialized applications like aerospace or marine engineering.
What is the melting point of pure aluminum?
+Pure aluminum melts at approximately 660°C (1220°F). (aluminum properties,melting point of aluminum)
How do alloying elements affect aluminum’s melting point?
+Elements like copper and silicon lower the melting point, while magnesium can increase it. (aluminum alloys,alloying elements)
Why is knowing the melting point important for welding?
+Precise temperature control during welding prevents weakening of the alloy. (welding aluminum,aluminum welding tips)
Understanding aluminum alloy melting points is key to leveraging their full potential. Whether for industrial or personal projects, this knowledge ensures efficiency, safety, and durability.